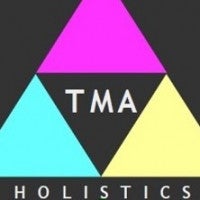
Where is your bottleneck?
The Story
Many moons ago, I happened to speak to a member of the top management of a large manufacturing company. Our topic was something dubbed “standard working hours decrease with compensatory wage increase”, in other words, working less hours per week while maintaining the pay.
The intent by the people that had initiated it was to help decrease unemployment figures during challenging economic times by creating additional jobs. In theory, reducing the weekly hours worked by 19 people by 2 per person would create one new, fulltime job, thus equaling about 365 new jobs for just that one manufacturing company...
So, how many new staff got hired? Well, hardly anyone.
Employers unsuccessfully scouring the labour market for, say fitters or turners are unlikely to hire accountants or nurses instead.
Effectively having to pay more for those on board already calls for an equivalent prior to any additional hire.
Therefore, their approach was more along the line “How can we achieve current output with current staff in less time?”
The Consideration
Outbound activity, such as improving sales or developing new markets, didn't appear to provide the right answers.
Inbound activity, on the other hand, looked promising with productivity taking centre stage.
The two options here were
- increasing output while maintaining input, or
- maintaining output with decreased input.
Since the situation rather called for the latter, looking for bottlenecks and road blocks to eliminate waste was considered appropriate. Either way, the focus would be on internal activities.
The Key Question
Within the next 12 months, which corrective action would yield how much cost benefit?
The Assessment
Any assessment would ask for some data acquisition prior to making a decision, and productivity assessments are no different. This data can be acquired by combing through areas that are either within or associated to the business.
Skills
People hired for a particular job bring a certain skill set. Topping up and/or updating these skills might help boost performance and productivity.
Equipment
There is obviously an advantage in using the tools or machinery that are best suited for the job on hand. Note that best suited does not necessarily mean the latest stuff.
Process
Any business activity should follow a process that could be tried, tested and reviewed regularly to identify opportunities for improvement. Even seemingly tiny things may have an impact. An airline decided to remove one olive from a salad served inflight. No one even noticed but it saved them about $40k per year.
Outsourcing
In average, about 30 production hours are required per one car at the original manufacturer. This is feasible due to components such as dashboards being pre-fabricated elsewhere and delivered on time straight to the assembly line.
Automation
An array of robots to weld or spray car bodies is a proven way to keep quality high and manufacturing cost steady.
Logistics
Components are supplied in time and to the right location on the premises, to save on cost for stock-keeping and internal transport. In addition, components might not incur procurement cost until delivered and accepted.
Communication
Effective communication has to happen from sourcing relevant materials to finished goods leaving the premises. While identifying bottlenecks and realising cost savings might be a challenge, it might be well worth the while.
Obviously, there are many more areas to potentially delve into...
Technology
Model range
Process design
Standardisation
Labelling
Quoting
Handling
Materials procurement
Wastage of raw materials
Asset maintenance
Accounting
...
One thing all these areas have in common: On your productivity gains journey, you want to ensure you don't pay Peter by robbing Paul. In other words, savings in one area are not really effective if they incur expenses in another. Therefore, it is good practice to look at neighbouring areas instead of assessing just one in isolation. This will help not losing sight of the big picture as well as with determining the most auspicious corrective action(s).
It is also worth noting that you can go on your productivity journey virtually anywhere. While assessing some remote manufacturing site might prove beneficial, looking at the more immediate administration site may also yield positive results.
The How-To
Questions to help getting started include
What would be the most promising area to get started with?
What would my goal be with respect to cost savings?
What particular activities are carried out in this area ?
How is an activity synchronised with a preceding or consecutive activity?
What makes an activity vital to the area's purpose or projected goal?
How can a vital activity be optimised or streamlined?
How big would the savings be?
How can a non-vital activity be made redundant? If you can't find any – look harder.
How much could be saved by doing that?
What would be the upstream/downstream effects of seizing it?
Please note that
1) “activity” can also mean something that happened in the past, is now static but still has an impact (see the olive example above),
2) “non-vital” is a property that is present but might not be required.
So, how many areas are too many, or not enough? How many activities can one handle? How many topics (or key factors) do I need to consider?
There is no one-number-fits-all answer to these questions.
From experience, starting with up to 3 areas in total when hunting for productivity gains will generally prove satisfactory, without being too overwhelming.
For example, assess one clearly defined area and include one upstream and one downstream area. Any area associated with significant cost has a good chance for notable gains.
Area size matters a lot, too.
For instance, if you have multiple lines for processing and packing cheese, start with one line only, or perhaps just with the packaging function of it. Thus, you're dealing with a relatively small and clearly arranged area, plus, have the additional benefits of getting quick results and gaining experience in the process.
As for timeframe, there is no one-number-fits-all answer either.
Assessing an area might take anything between a day or a month. Determining corrective activities, their implementation, and following up on their effectiveness might take anything from one week to six months.
When it comes to determining topics (or key factors) relevant to the chosen areas, they should relate to potential cost savings since this is what productivity gains is about.
Phrasing a question rather than a statement for a key factor will get you an answer you can base a corrective action on.
Corrective actions require resources, for scoping, planning, implementation, and review. Hence, ensure you adjust the number of key factors (and subsequent corrective actions) to suit your resources – or vice versa.
In the end, a number of 1 or 2 successfully implemented corrective actions is much more favourable than coming up with half a dozen that stretch your resources too thinly. There will be another opportunity, just a bit later, to implement another corrective action successfully.
Moreover, keep in mind that changes to one area might not show any effects there but affect upstream or downstream areas.
The Action
Making productivity gains is a long-term string of activities. After all, it is just a specific kind of continuous improvement, and, like the CI LOOP, it is regular round trips delivering new results each time you embark on that journey.
Productivity gains are made through particular actions based on and determined by facts, they need to be followed up and reviewed regularly and frequently.
While there are many different ways to go about productivity gains, the following pattern may serve as a rough guideline.
1) Choose 1 main and 2 neighbouring areas
2) Determine the topics to assess (at least 2, no more than 4)
3) Get the data. Try to translate everything into one specific unit (e.g. $$)
4) Create a table for areas and topics, enter the data and analyse it
5) Determine the highest potential saving (max. 1 per area), the corrective activity required, and potential gains (saving - cost)
6) Implement corrective action and monitor to check if gains are consistent and as expected
7) Tweak action(s) if required
Last But Not Least
Remember that making productivity gains is a team effort. Travelling as a party will be more inspiring than doing the journey alone.
In fact, talking and listening to people involved in the particular area will be mission-critical right from the start.
Hunting for productivity gains (and introducing new things in the process) might spell change, so some people who are directly involved or concerned might be a lot less enthusiastic about it. Therefore, support from people who are not directly involved might be mission-critical as well...
How is your productivity?
#waste #savings #productivity #gains #services #reliability #TPM #tmaholistics
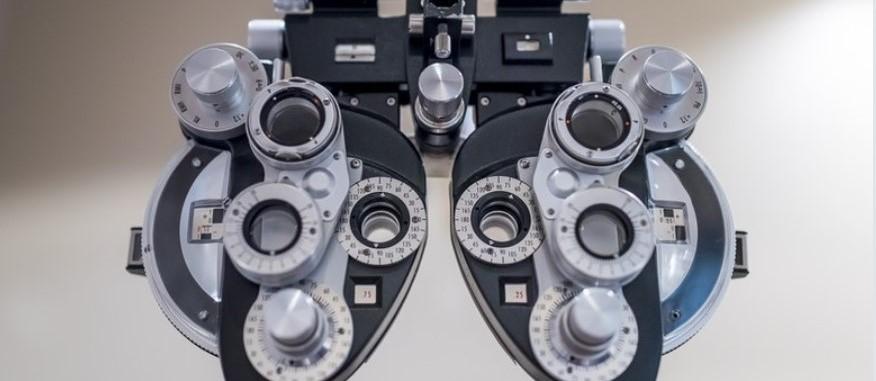

Live Q&A: Garden maintenance with Crewcut
This Wednesday, we are having another Neighbourly Q&A session. This time with John Bracewell from Crewcut.
John Bracewell, former Black Caps coach turned Franchisee Development Manager and currently the face of Crewcut’s #Movember campaign, knows a thing or two about keeping the grass looking sharp—whether it’s on a cricket pitch or in your backyard!
As a seasoned Crewcut franchisee, John is excited to answer your lawn and gardening questions. After years of perfecting the greens on the field, he's ready to share tips on how to knock your garden out of the park. Let's just say he’s as passionate about lush lawns as he is about a good game of cricket!
John is happy to answer questions about lawn mowing, tree/hedge trimming, tidying your garden, ride on mowing, you name it! He'll be online on Wednesday, 27th of November to answer them all.
Share your question below now ⬇️
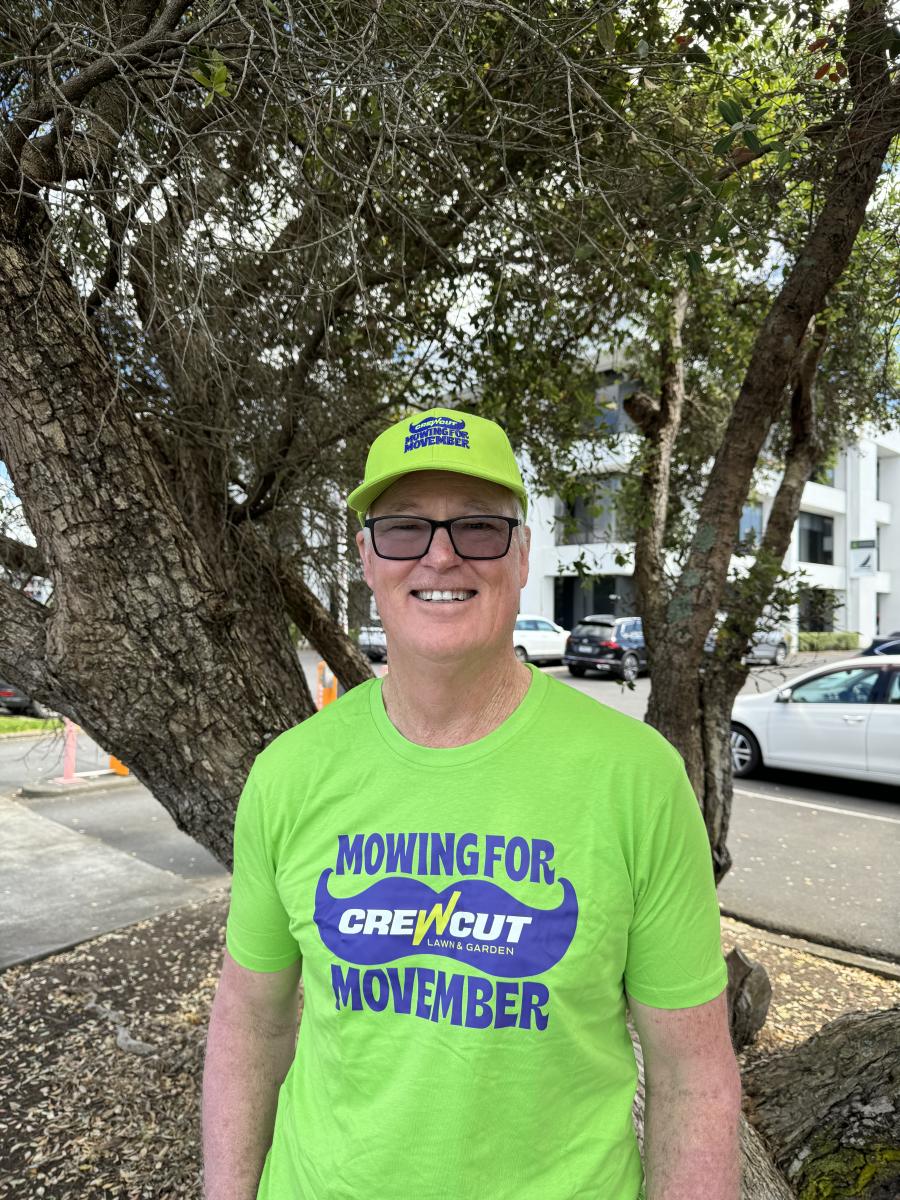

Poll: Should all neighbours have to contribute to improvements?
An Auckland court has ruled a woman doesn’t have to contribute towards the cost of fixing a driveway she shares with 10 neighbours.
When thinking about fences, driveways or tree felling, for example, do you think all neighbours should have to pay if the improvements directly benefit them?
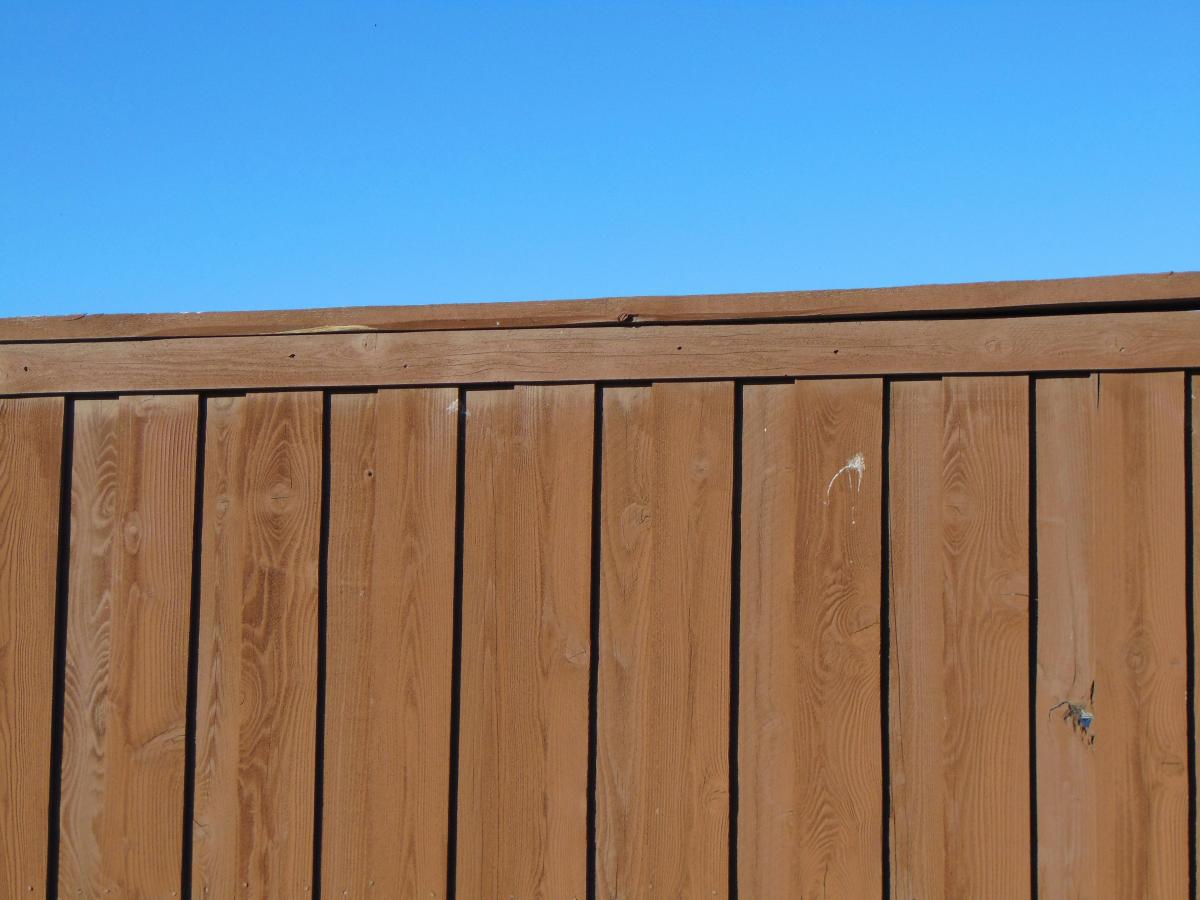
-
82.7% Yes
-
14.8% No
-
2.5% Other - I'll share below

What's your favourite recipe for courgettes?
Kia ora neighbours. If you've got a family recipe for courgettes, we'd love to see it and maybe publish it in our magazine. Send your recipe to mailbox@nzgardener.co.nz, and if we use it in the mag, you will receive a free copy of our January 2025 issue.
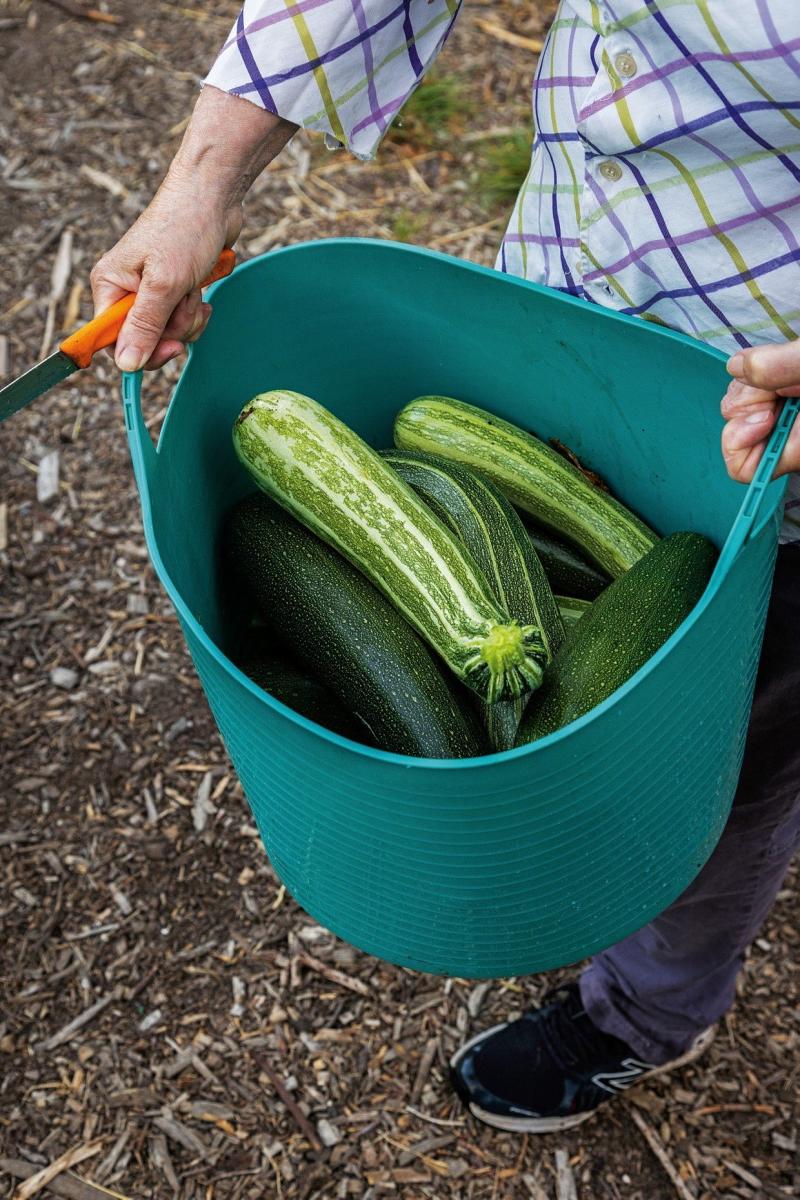